CERMAT2 Winter School 2015, February 2-12, 2015, Trento
![]() |
TC2 "Introduction to virtual prototyping" (20hrs) The programme of the course tackles both enabling technologies in the field of scientific computing (numerical grid generation, finite elements, finite difference and finite volume methods, higher order methods) and a number of important applications (flow processes, design of new materials, subsurface flow, aero-acustics, agro-food technology, large scale industrial applications) to advance knowledge in a wide range of technical processes and physical phenomena of very high societal interest.
WS1 "Workshop on state-of-the-art and challenges in the modern Ceramic Technology"
Flyer
Download flyerVenue
The CERMAT2 Winter School will take place at the Department of Civil, Environmental and Mechanical Engineering of the University of Trento (via Mesiano, 77). The Department is located on a beautiful hill, 10 minutes far from Trento city center by taking bus N.5 at the train station.How to reach us
Registration Form
You are not required to pay application or tuition fees. Registrations to the event are open until we reach a limited number of participants. Please send this registration form duly filled in together with your CV to Miss. Irena Jatro (irena.jatro@unitn.it)Download the Registration Form
Programme - TC1 - February 2-6, 2015
TC1 - Topics in constitutive modelling of frictional materials: theory and automation of numerical implementation of plasticity at small and large strains (36hrs)(Prof. Jože Korelc, Prof. Stanisław Stupkiewicz)
The course will consist of two interlinked parts: constitutive modelling in mechanics of materials and automation of numerical implementation of the constitutive models. The main focus of the first part will be elastoplasticity at small and finite strains. The fundamental concepts of continuum mechanics will be introduced as a basis for a systematic presentation of several constitutive models. The topics covered will include elasticity, elastoplasticity with isotropic and kinematic hardening and coupled thermoplasticity, as well as selected specialized models such as crystal plasticity. In addition to the usual formulation of each model, it will be shown how to formulate the model in a way that the advanced automation tools discussed in the second part of the course can be efficiently used for its numerical implementation. Considering numerical implementation, a general structure of incremental constitutive equations and return mapping algorithm will be introduced.
The second part of the course will first address the broad area of advanced software technologies for scientific computing. It will be demonstrated that an efficient automation of a general formulation of plasticity models can be achieved using the automatic differentiation technique combined with the symbolic problem description, automatic code generation and code optimization. The main objective of the course is to provide theoretical background as well as practical practical training for automatic generation of nonlinear finite element codes using Mathematica based code generation system AceGen (www.fgg.uni-lj.si/symech/). Participants will get insight into the mathematical formulation of a problem, its symbolic description with symbolic code generator AceGen, methods for verification of the model and the generated code and a final implementation in the finite element environment AceFEM and ABAQUS. The advantages of using automatic differentiation technique and symbolic description of plasticity models will be demonstrated on several examples including: hyperelasticity, finite-strain plasticity, coupled thermo-mechanical problems and multi-scale analysis. The lectures will be given in computer laboratory. Students will be encouraged to try to use symbolic approach on their specific field of research. All the participant will get students AceGen/AceFEM license and lecture notes.
Classroom - equipped with blackboard and computer projector.
Computer laboratory - The lectures will be given in a computer laboratory. All the participants will get students AceGen/AceFEM licence. Students that will use their own notebook must have symbolic system Mathematica version 9.0 or 10.0 preinstalled.
The division of the topics into individual time slots is provisional.
Monday, February 2, 2015
09:00-12:30 Classroom (S.S. and J.K.)
* | Introduction: motivation, problems, solutions (S.S. and J.K.) |
* | Introduction to continuum mechanics (small and finite strain) |
* | Hyperelasticity |
MATERIAL
14:00-17:30 Computer lab (J.K.)
* | Introduction to advanced software technologies in computational mechanics |
* | Symbolic systems, hybrid systems, automatic generation of numerical codes, expression swell problem, code optimisation, brief introduction to Mathematica |
* | AceGen: hybrid symbolic-numeric system for multi-language and multi-environment generation of numerical codes, introductory example |
MATERIAL
Tuesday, February 3, 2015
09:00-12:30 Computer lab (J.K.)
* | Introduction to automatic differentiation, theory of automatic differentiation and various implementations |
* | Automatic differentiation based notation of numerical problems, example of isoparametric mapping, general formulation of direct and sensitivity analysis of coupled path-dependent problems |
* | AceFEM: hybrid symbolic-numeric finite element environment, simple example of isoparametric, 2D, Neo-Hooke element |
MATERIAL
14:00-17:30 Classroom (S.S.)
* | Hyperelasticity (continued) |
* | Model problem: elastoplasticity in 1D and small strain |
* | Basic numerical methods in nonlinear solid mechanics (Euler method, Newton method, finite element discretization) |
MATERIAL
Wednesday, February 4, 2015
09:00-12:30 Classroom (S.S.)
* | Elastoplasticity at small strain (constitutive equations, thermodynamic setting) |
* | Elastoplasticity at small strain (rate and incremental formulations) |
* | Return mapping algorithm and constitutive update problem |
MATERIAL
14:00-17:30 Computer lab (J.K.)
* | Examples and implementation of plasticity models: Mises, forward and backward Euler |
* | Advanced element formulations: mixed elements, EAS, B-bar, etc. |
* | Matrix functions, eigenvalues, functions with singularities, ... |
MATERIAL
- Hyperelastic_AceFEM_T15_Wednesday.pdf
- Hyperelastic_AceFEM_T15_Wednesday.nb.pdf
- Hyperelastic_AceFEM_T15_Wednesday.nb
Thursday, February 5, 2015
09:00-12:30 Classroom (S.S.)
* | Elastoplasticity at finite strain |
* | Specialized models: crystal plasticity |
* | Coupled thermoplasticity at small strain |
MATERIAL
14:00-17:30 Computer lab (J.K.)
* | Validation and verification of numerical codes, debugging of automatically generated codes |
* | Multi-field problems: solution strategies (monolithic, staggered) , example: elastic thermo-mechanically coupled element |
* | Multi-field problems: fully coupled thermoplasticity element |
MATERIAL
Friday, February 6, 2015
09:00-12:30 Classroom (S.S. and J.K.)
* | Introduction to micromechanics: macroscopic quantities, Hill's lemma, boundary conditions |
* | Micromechanics: extension to finite strain and FE^2 approaches |
* | ADB formulation of FE^2, AceGen implementation, examples (J.K.) |
MATERIAL
14:00-18:30 Computer lab (J.K. and S.S.)
* | Individual exercises and consultations: each participant will symbolically formulate and obtain prototype solution of a problem related to its specific field of research or optionally of a problem given by the lecturers. |
MATERIAL
Programme - TC2 - February 9-11, 2015
TC2 - Introduction to virtual prototyping (18hrs)(Prof. Stefano Odorizzi)
The programme of the course tackles both enabling technologies in the field of scientific computing (numerical grid generation, finite elements, finite difference and finite volume methods, higher order methods) and a number of important applications (flow processes, design of new materials, subsurface flow, aero-acoustics, agro-food technology, large scale industrial applications) to advance knowledge in a wide range of technical processes and physical phenomena of very high societal interest.
Monday, February 9, 2015
08:30-12:30 - 14:00-18:00
The Finite Elements Method for structural analysis (Prof. Stefano Odorizzi, 8 hours)
- Theory of elasticity: summary, assumptions and definitions
- Considerations over the stress formulation
- Displacement formulation of the FEM
- Direct formulation of a finite element
- Shape functions and finite elements families
- Curve and parametric coordinates
- Transformations
- Considerations over numerical integration
- Characteristics of the resulting equations
- Computation of displacements and forces
- Loads
- Merge
Tuesday, February 10, 2015
08:30-12:30
Applications (Eng. Vito Boriolo, 4 hours)
- FEM method applied to thermal analyses: brief description
- Examples of steady state and transient thermal problems and solution methods
- Examples of application in the Oil & Gas sector (thermo-structural analyses, seismic analyses, fracture mechanics, creep)
14:00-18:00
Applications (Eng. Maurizio Facchinetti, 4 hours)
- FEM Method applied to flow processes of non-Newtonian fluids (e.g. polymers)
- Basic Equations: mass, momentum and energy conservation
- Polymers properties: brief description
- Application examples: extrusion process; injection moulding; blow molding and thermoforming
- Structural analyses on molds and on polymer parts
Wednesday, February 11, 2015
08:30-12:30
Applications (Eng. Alessio Trevisan, 4 hours)
- Examples of applications to the civil and mechanical engineering sector
- Examples of non-linear problems and solution methods
- Examples of dynamic problems and solution methods
Programme - WS1 - Thursday, February 12, 2015
WS1 Workshop on state-of-the-art and challenges in the modern Ceramic TechnologyMorning session, general lectures.
8:40-9:40 "Chemically-bonded ceramics and composites: materials, processes and applications"
Valentina Medri, Alida Bellosi, ISTEC-CNR, Faenza, Italy
9:40-10:40 "State of the art and future trends in the industrial production of ceramic tiles"
Alessandro Cocquio, SACMI Imola SC, Imola, Italy
10:40-11:10 Coffee break
11:10-12:40 "Technology of tetragonal zirconia polycrystals and related ceramics"
Waldemar Pyda, AGH University of Science and Technology, Krakow, Poland
12:40-14:00 Lunch
Afternoon sessions, PhD students presentations.
14:00-15:00
- ESR1 Scot Swan:
"Models for Compaction of Granular Materials: Constitutive Modeling, Numerical Implementation, and Experimental Validation"
- ESR2 Aniss Kessaci:
"Optimal forming and sintering of ceramics compounds"
- ESR3 Gennaro Vitucci:
"Modelling of inhomogeneous prestressed multi-layer ceramic structures under mechanical loads and thermal expansion"
- ESR4 Anastasiya Vinakurava:
"Constitutive modelling of microstructural ceramics for bone replacement accounting for the tissue growth"
- ESR5 Nikolai Gorbushin:
"Fracture waves propagating in discrete structures with non-local interactions"
- ESR6 Domenico Tallarico:
"Development of mathematical models of the dynamic response of ceramic piezoelectric composite layered structures"
- ESR7 Mojtaba Biglar:
"Microstructural and strain analysis of damage processes taking place in neighborhood of defects in piezo- electric ceramic material"
- ESR8 Shwetank Pandey:
"Material Characterization using Inverse Analysis"
- ER1 Adrian Borhan:
"New elaborated glass materials for sealing ceramic oxygen membranes"
- Daria Andreeva (Aberysteyth University):
"Nonlinear transmission conditions for thin curvilinear low-conductive interphases in composite ceramics"
Teachers Profiles
![]() |
Prof. Stanisław Stupkiewicz. Stanisław Stupkiewicz is a professor at the Institute of Fundamental Technological Research (IPPT) of the Polish Academy of Sciences in Warsaw, Poland. He graduated from the Warsaw University of Technology in mechanical engineering and received his PhD (1996) and habilitation (2006) at IPPT. Since 2011 he is a full professor. For one year in 2013-2014, he was a visiting professor at the University of Trento in the Solid and Structural Mechanics Group. His research interests include micromechanics of interfaces and interface layers, multiscale modelling of shape memory alloys, constitutive modelling of contact phenomena, contact mechanics, sensitivity analysis, plasticity and computational mechanics. He is the author or co-author of about 50 papers published in high-rank journals and one book published by Springer. He is a Section Editor of the Archives of Mechanics journal. |
![]() |
Prof. Jože Korelc. Prof. Jože Korelc graduated from the University of Ljubljana and finished his PhD at the Darmstadt University of Technology. His research examines an interdisciplinary approach to computational mechanics as synthesis of classical numerical methods and symbolic-algebraic systems. He has published numerous articles on finite element technology for solid and contact problems, material modeling, sensitivity analysis, automatic code generation and the use of symbolic methods in engineering. Prof. Korelc is currently Head of the Division of Structures at the Faculty of Civil and Geodetic Engineering, University of Ljubljana, Vice-president of the Scientific Computing Committee of ECCOMAS and a primal developer of the software systems AceGen and AceFEM for on-demand numerical code generation and finite element analysis. |
![]() |
Prof. Stefano Odorizzi. Graduated in Civil Engineering in 1973, Stefano Odorizzi started his activity as researcher in 1976 at University of Padova, where he holds the course of Solid Mechanics. CEO and co-founder of EnginSoft, multinational consultancy company engaged in Simulation Based Engineering Science, he actively promotes numerical simulation for research activity, with particular attention for manufacturing process, metallurgy, multi-disciplinary and multi-objective optimization. Since 1977, he has been Project leader of a large number of EU co-funded research projects (like COMETT, CRAFT, BRITE-EURAM, MURST, EU-RTD); he is an active member of several associations (ISOPE, ASM Europe, AICAP, AIM, ATA, NAFEMS) and he plays an important role within prestigious European Networks (MACSinet, FENET, INGENET, TECHNET). His commitment in numerical simulation dissemination is witnessed by his many initiatives as General Manager of EnginSoft, in academic research and advanced training and education. |
![]() |
Eng. Vito Boriolo. Vito Boriolo is a Civil Engineer and FEM Project Engineer in Enginsoft, specialized in R&D industrial projects regarding: Oil and gas application (Pressure vessel, heat generators, reactors, Non conventional Creep verification, Nuclear plants, Check valves dynamics, seismic analyses), Turbomachinery applications (Blade creep verification), Automotive applications (Radiator fan dynamics, Vehicles axles structural vefication),Civil applications (structural requalification of nuclear power plants). |
![]() |
Eng. Maurizio Facchinetti. Maurizio Facchinetti is a Civil Engineer and Project Manager in Enginsoft, specialized in FEM analysis, mainly concerned with R&D industrial projects regarding: Nuclear and Oil&gas applications (High temperature/high pressure pressure vessel, heat generators, reactors, non conventional nreep verification, metal gasket flanges), Polymer processing applications (injection molding, extrusion, thermoforming, blow molding) in several industry sectors (Appliances, Automotive, Manufacturing), Rubber processing in the automotive industry, Multiphisics analyses on polymers parts and steel molds. |
![]() |
Eng. Alessio Trevisan. Alessio Trevisan is a Mechanical Engineer in Enginsoft, specialized in civil structures (seismic assessment), amusement structures (structural assessment of roller coaster and other attractions), offshore structures (structural assessment of jackets, pipes, nodes), large steel structures (stadiums, bridges, equipments), pressure vessels (structural assessment) rail cars (structural assessment). |
Photos
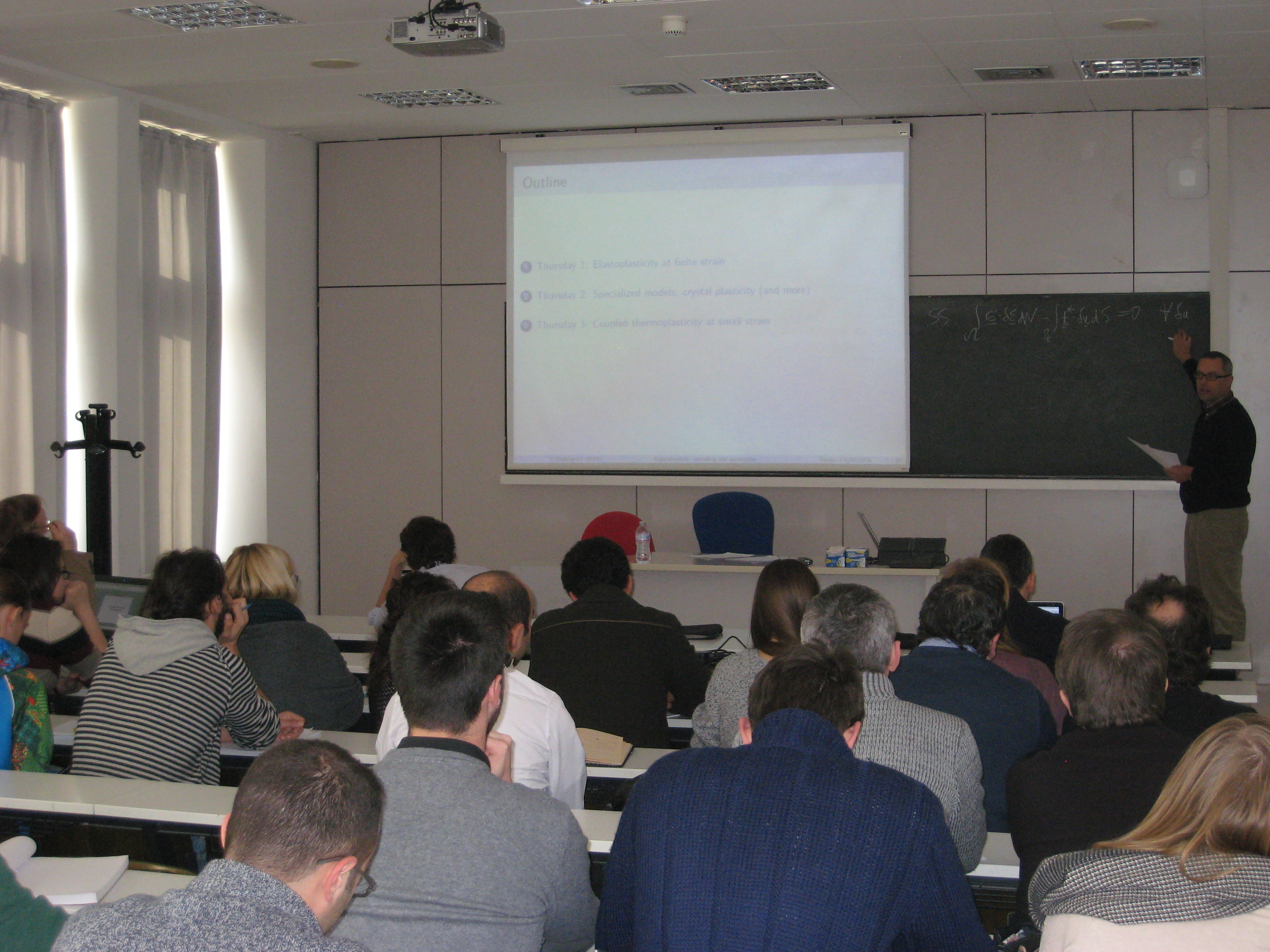
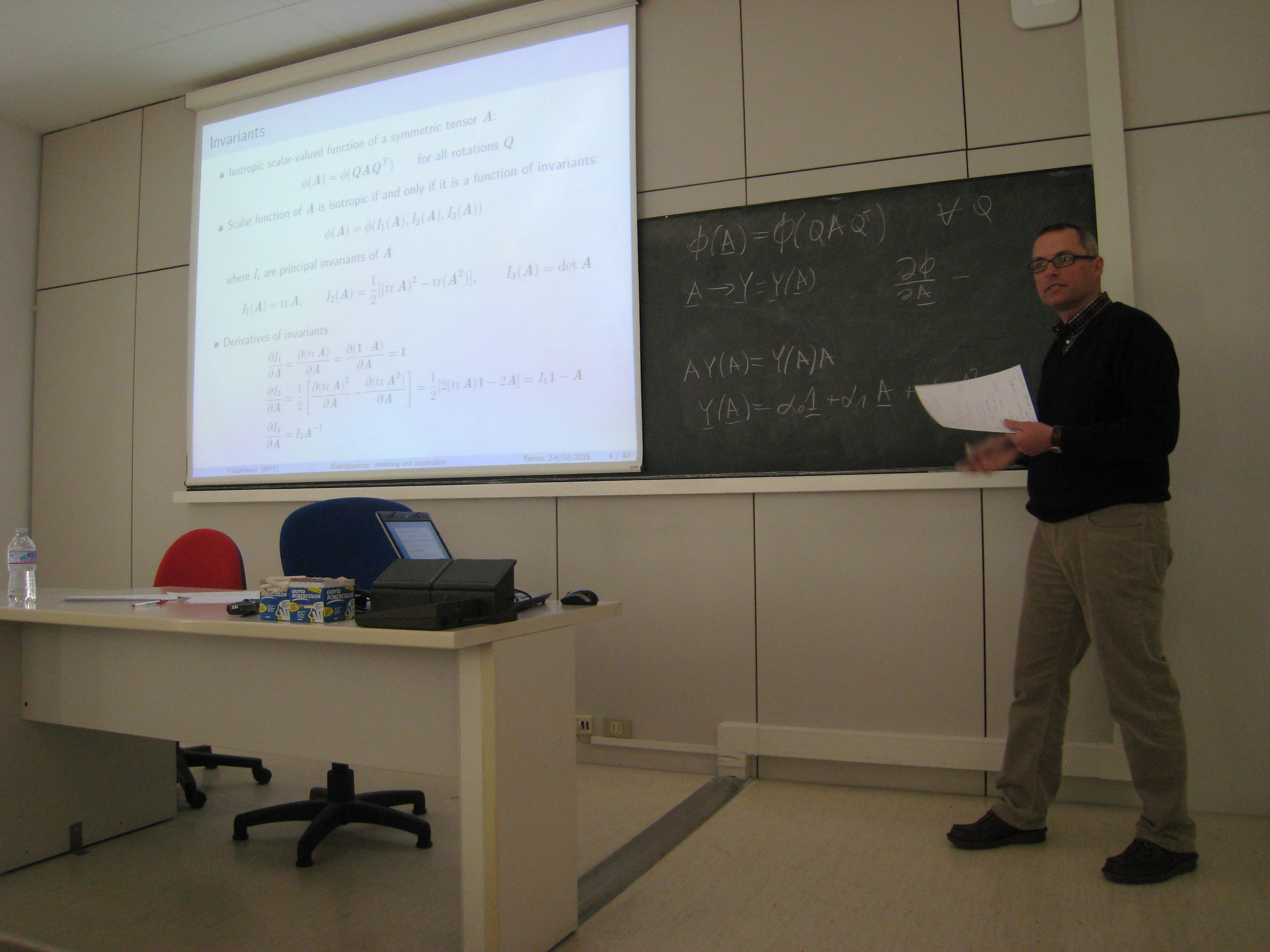
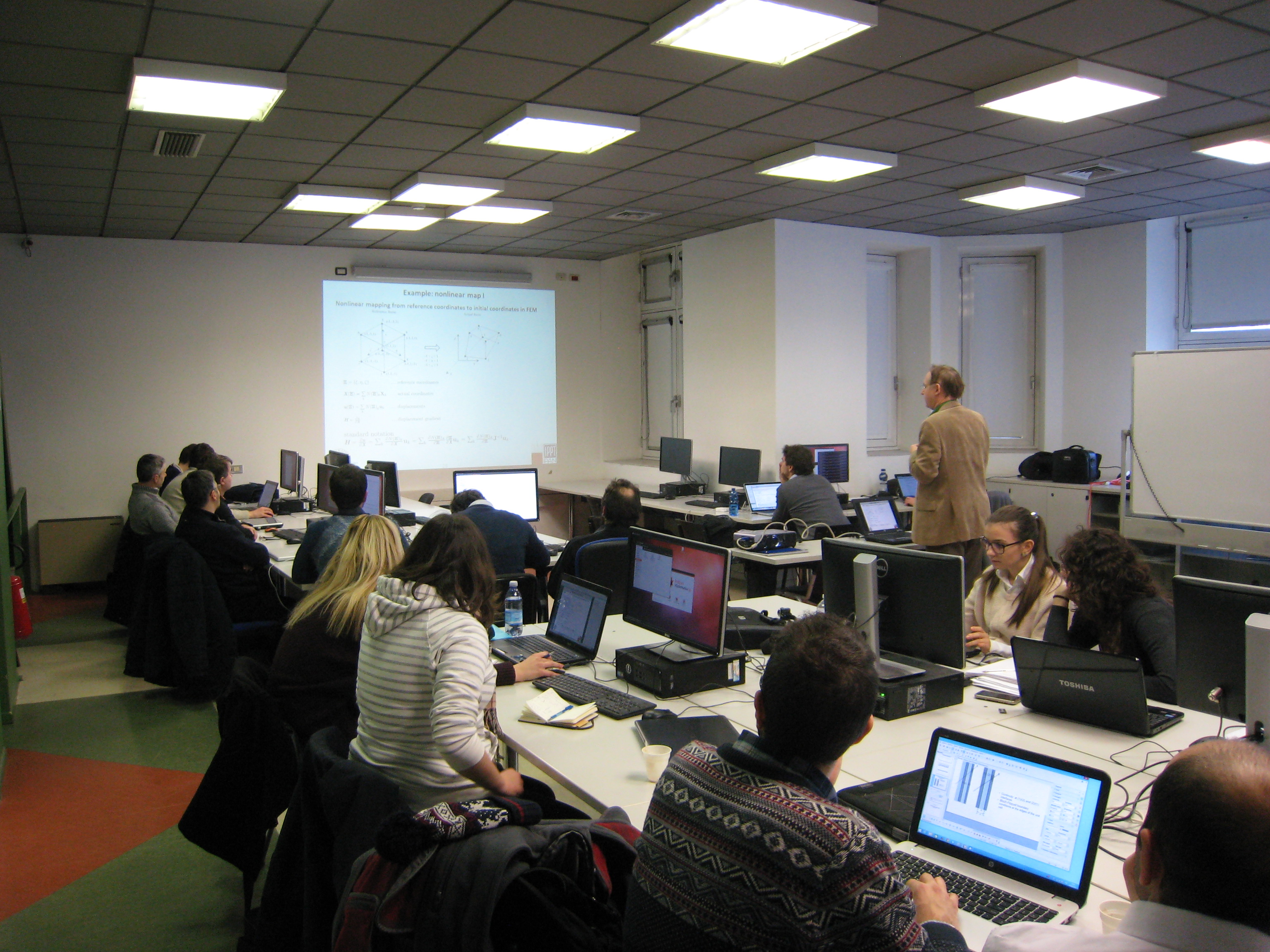
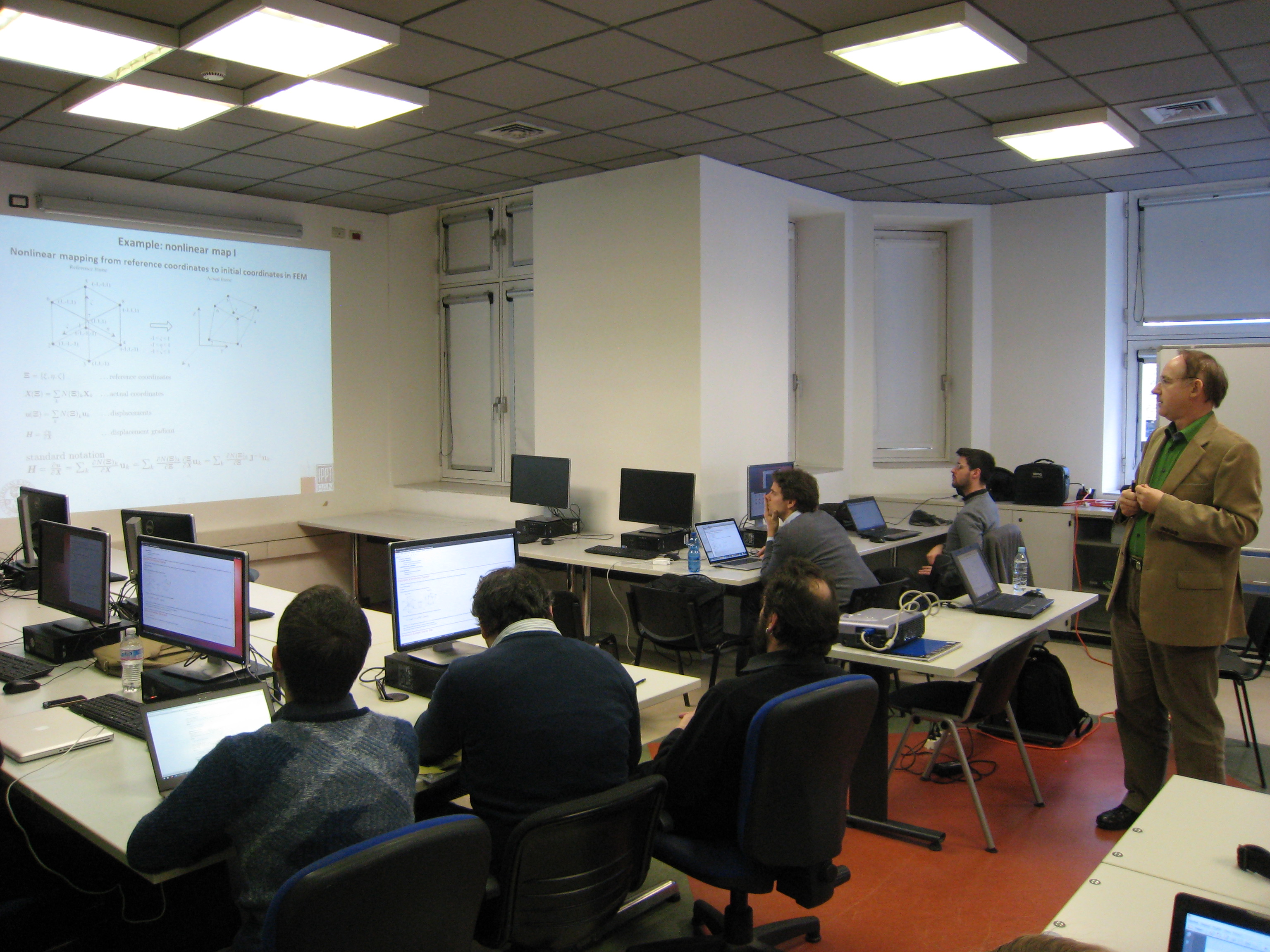
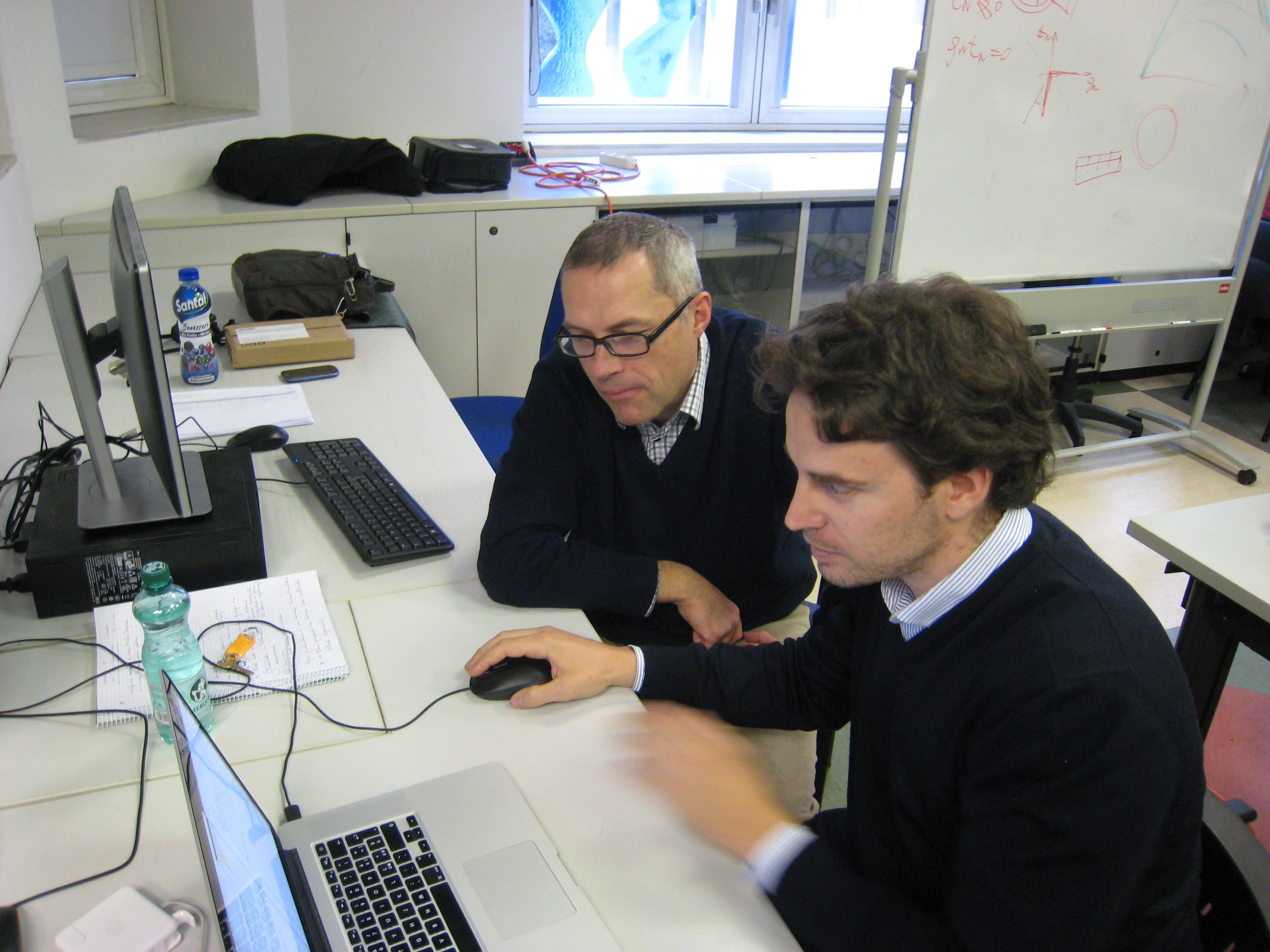
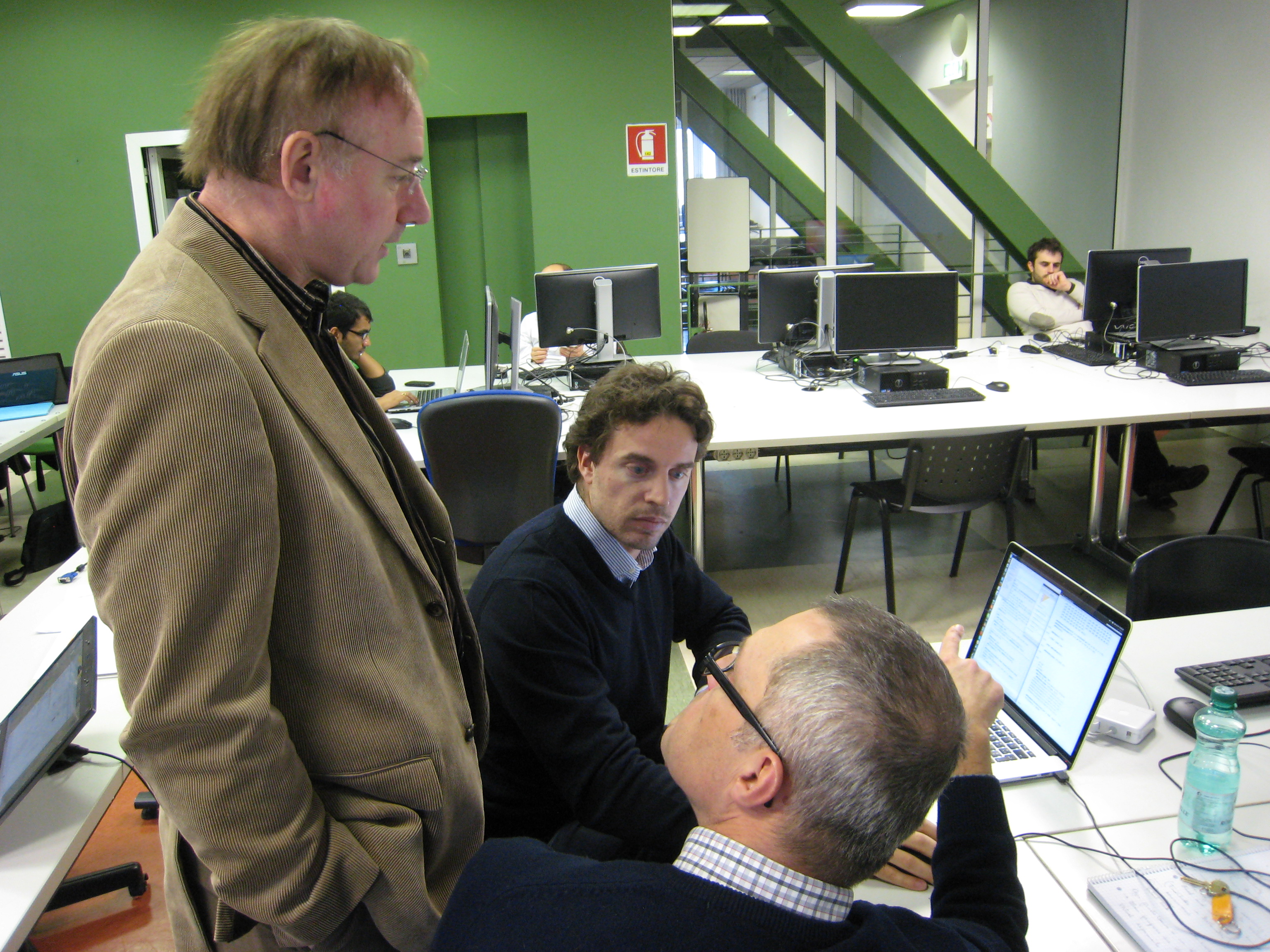
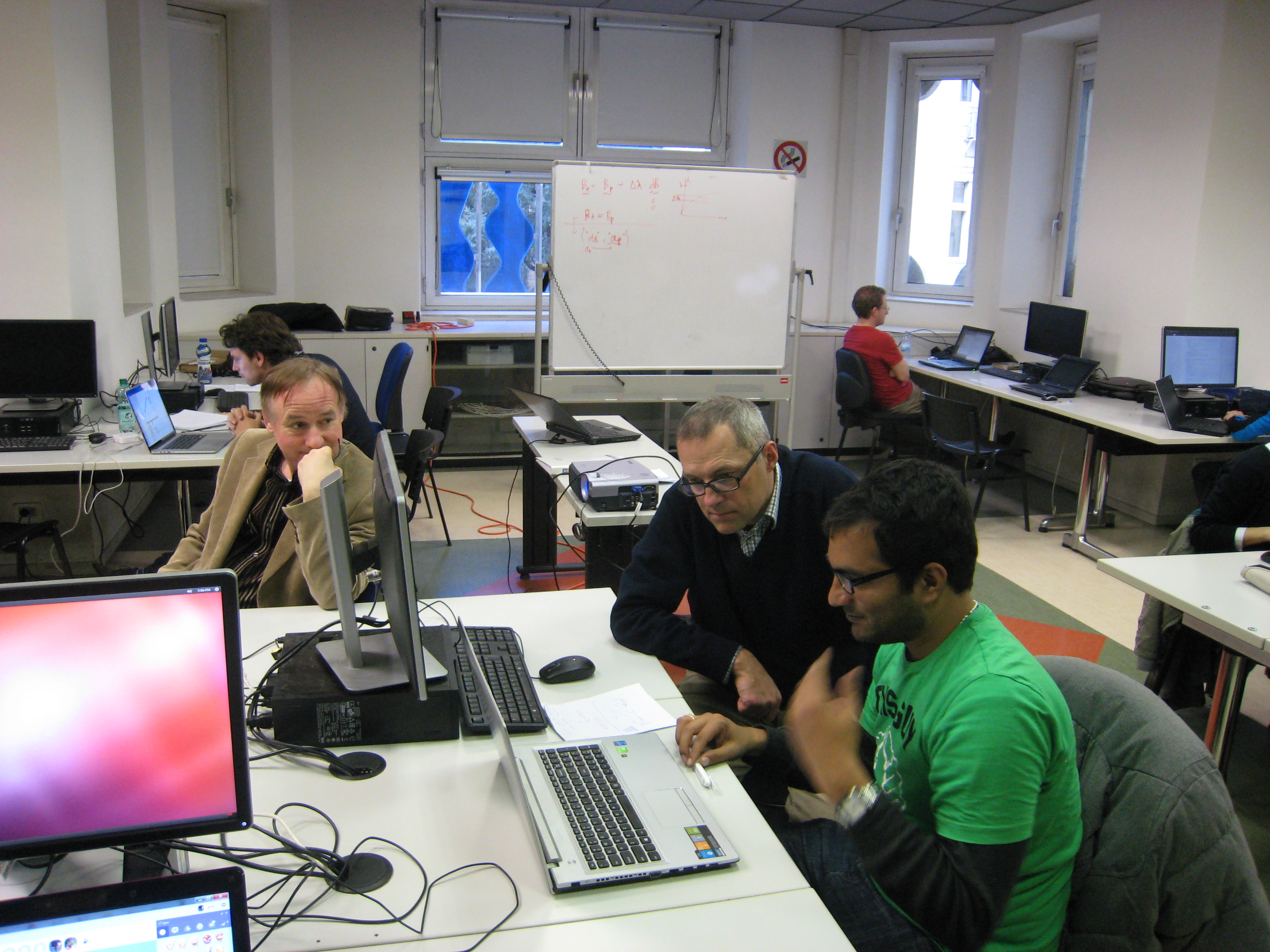
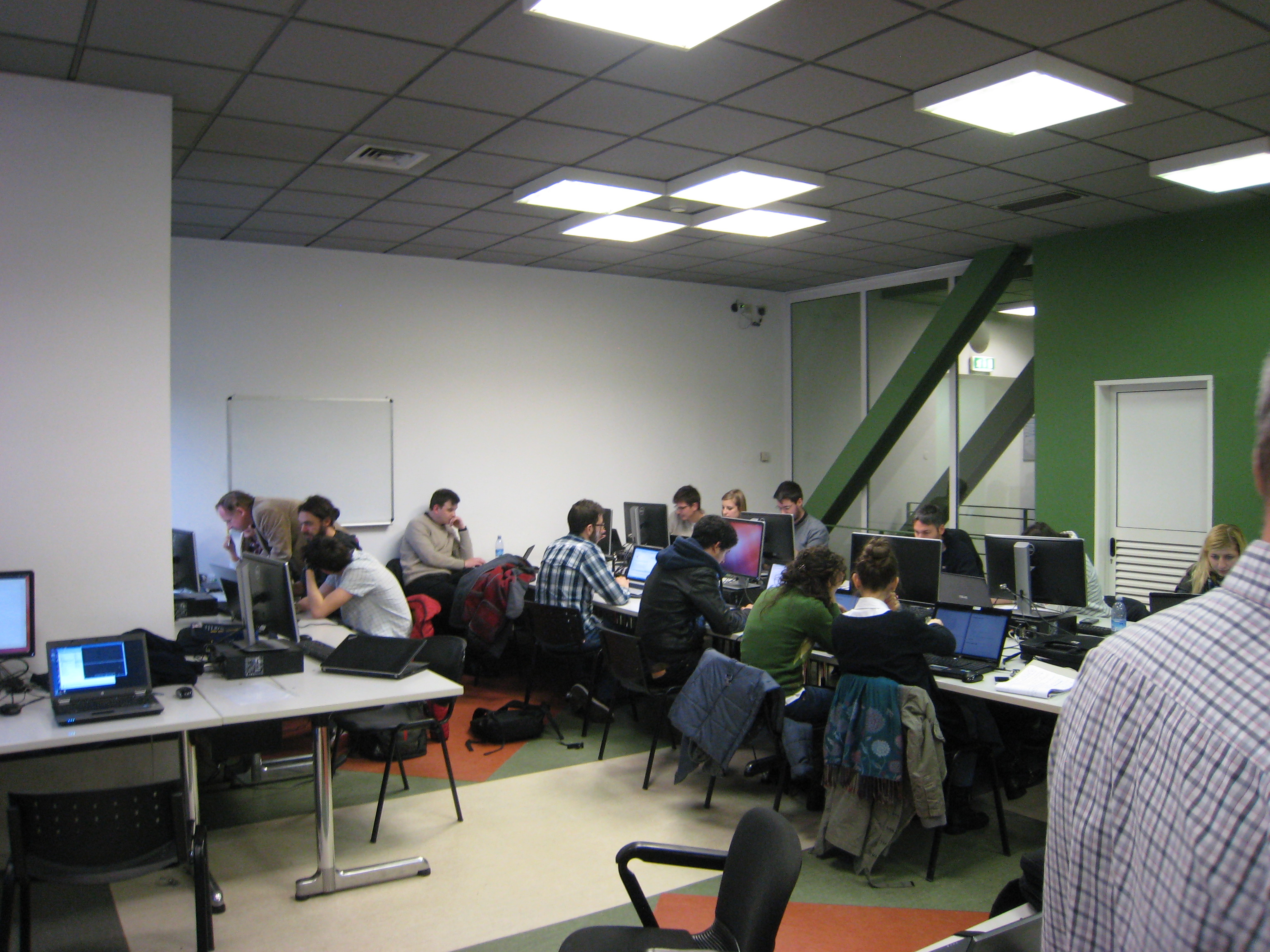
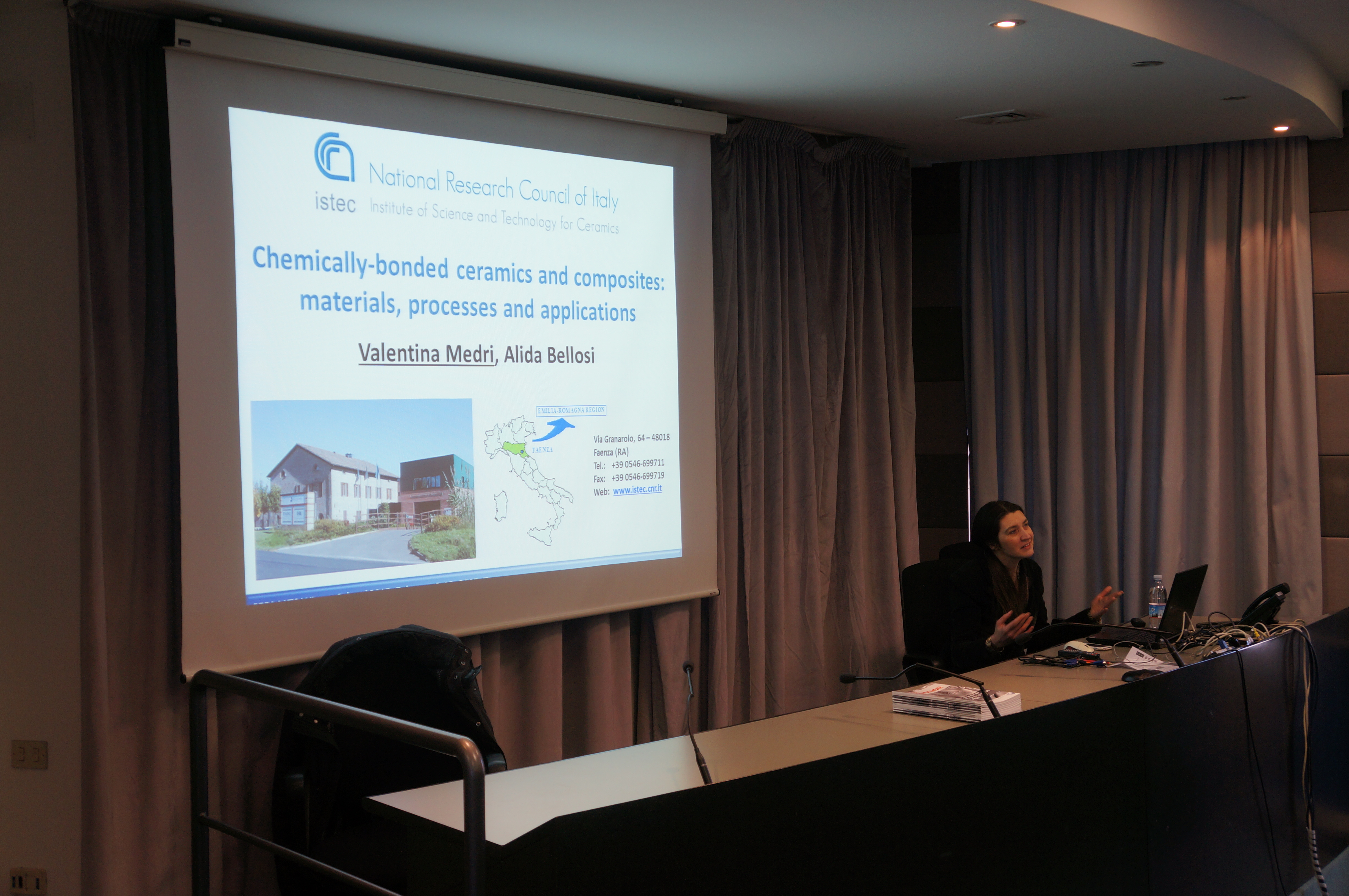
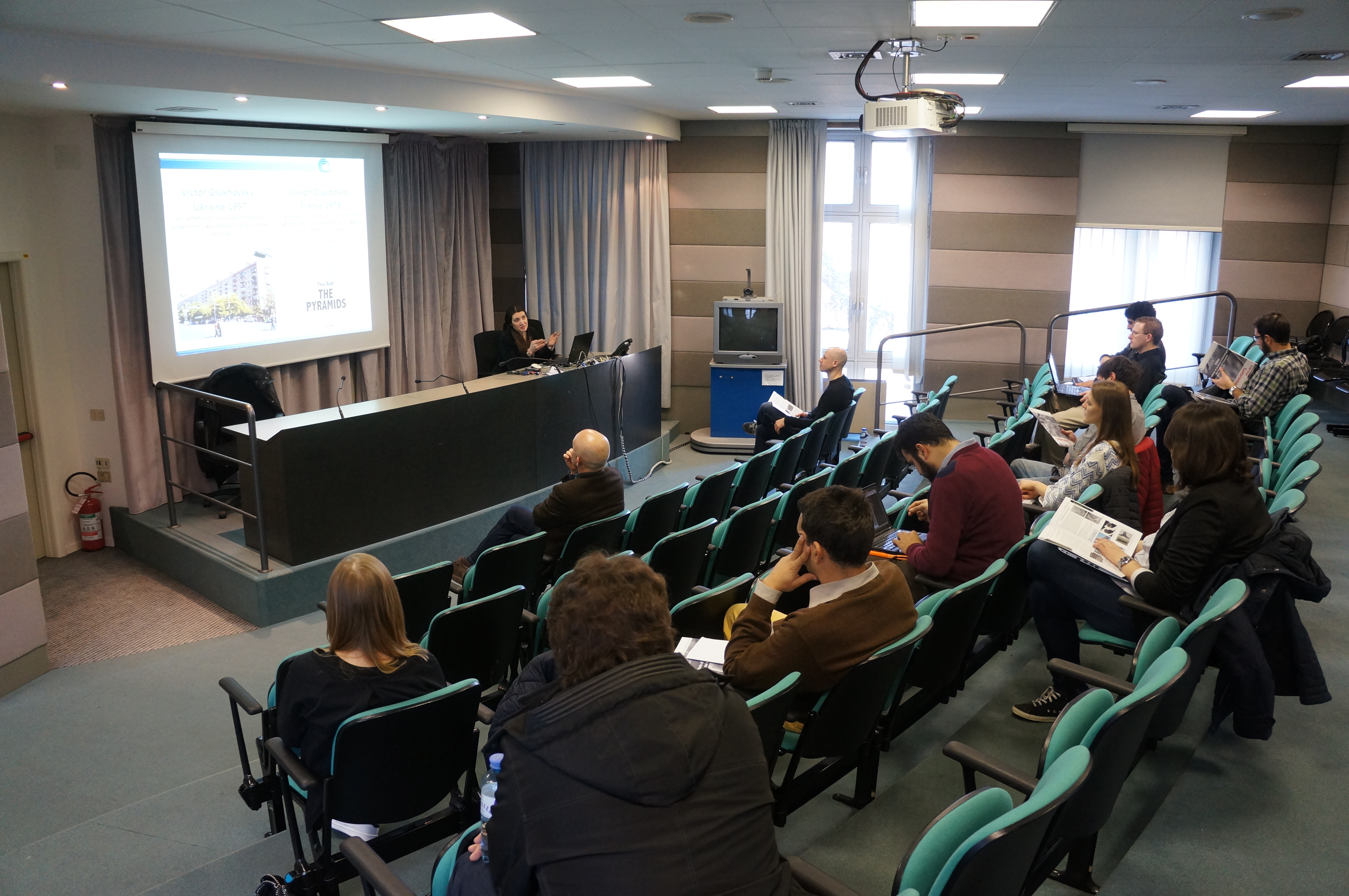
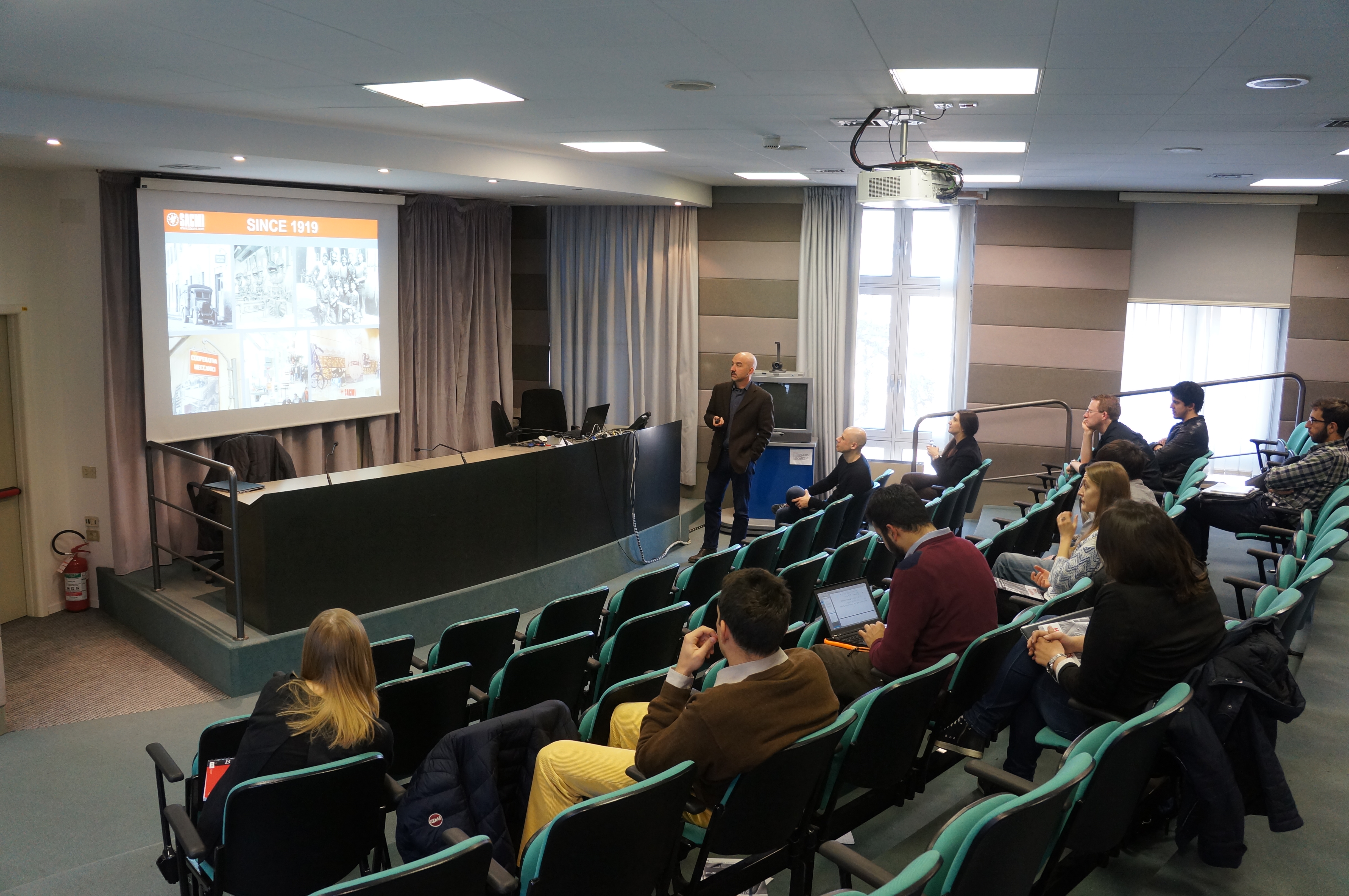
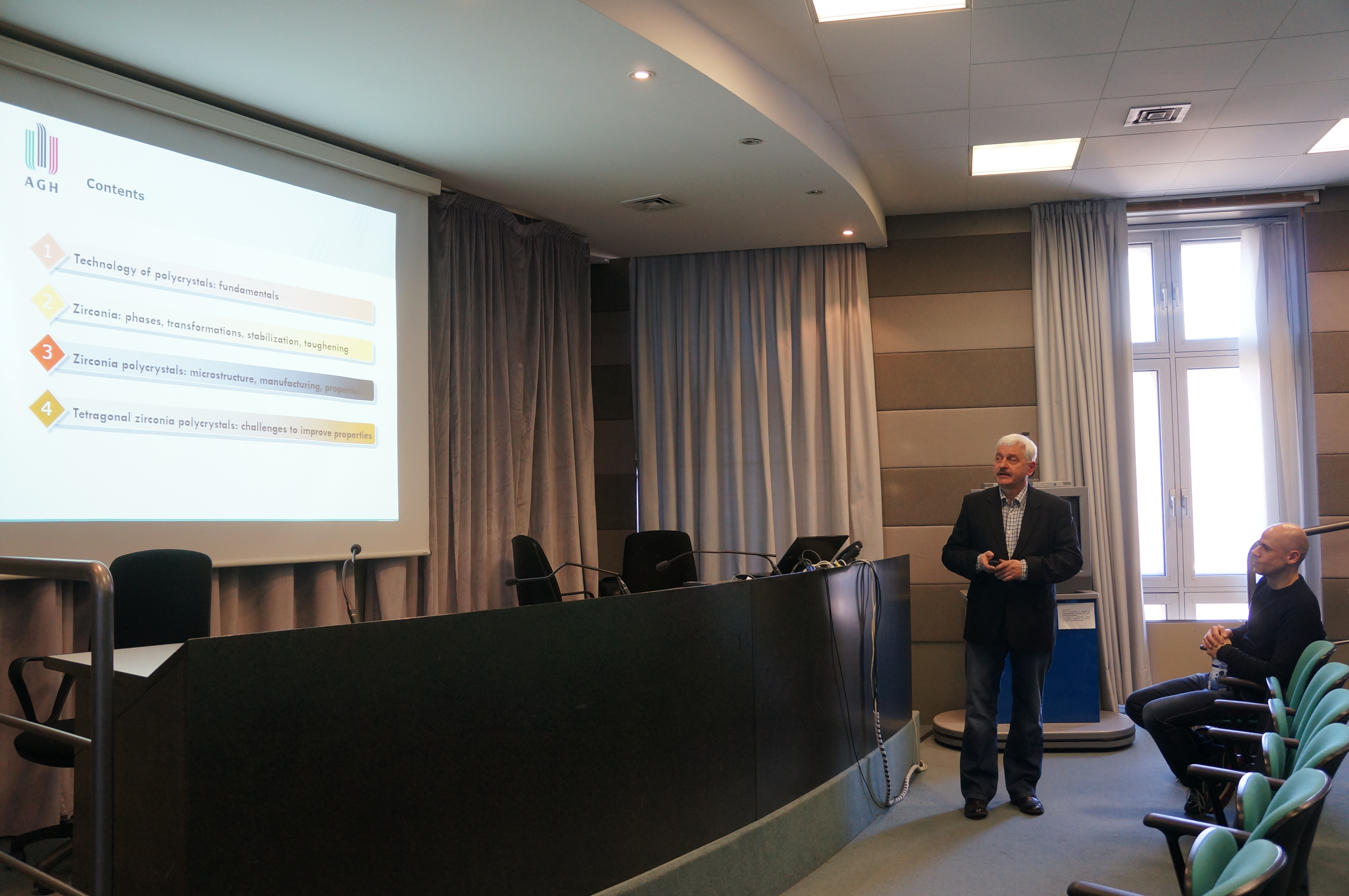
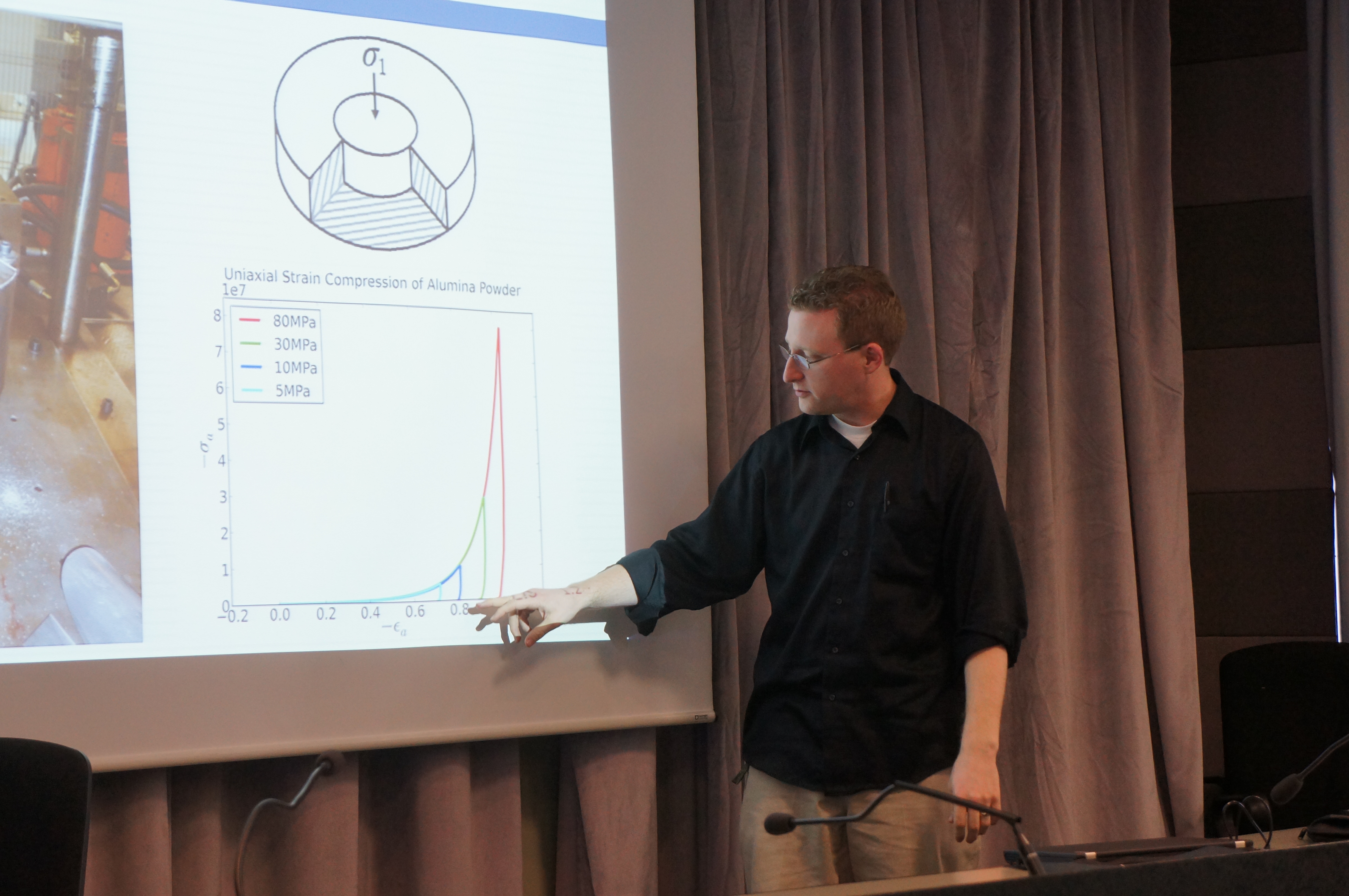
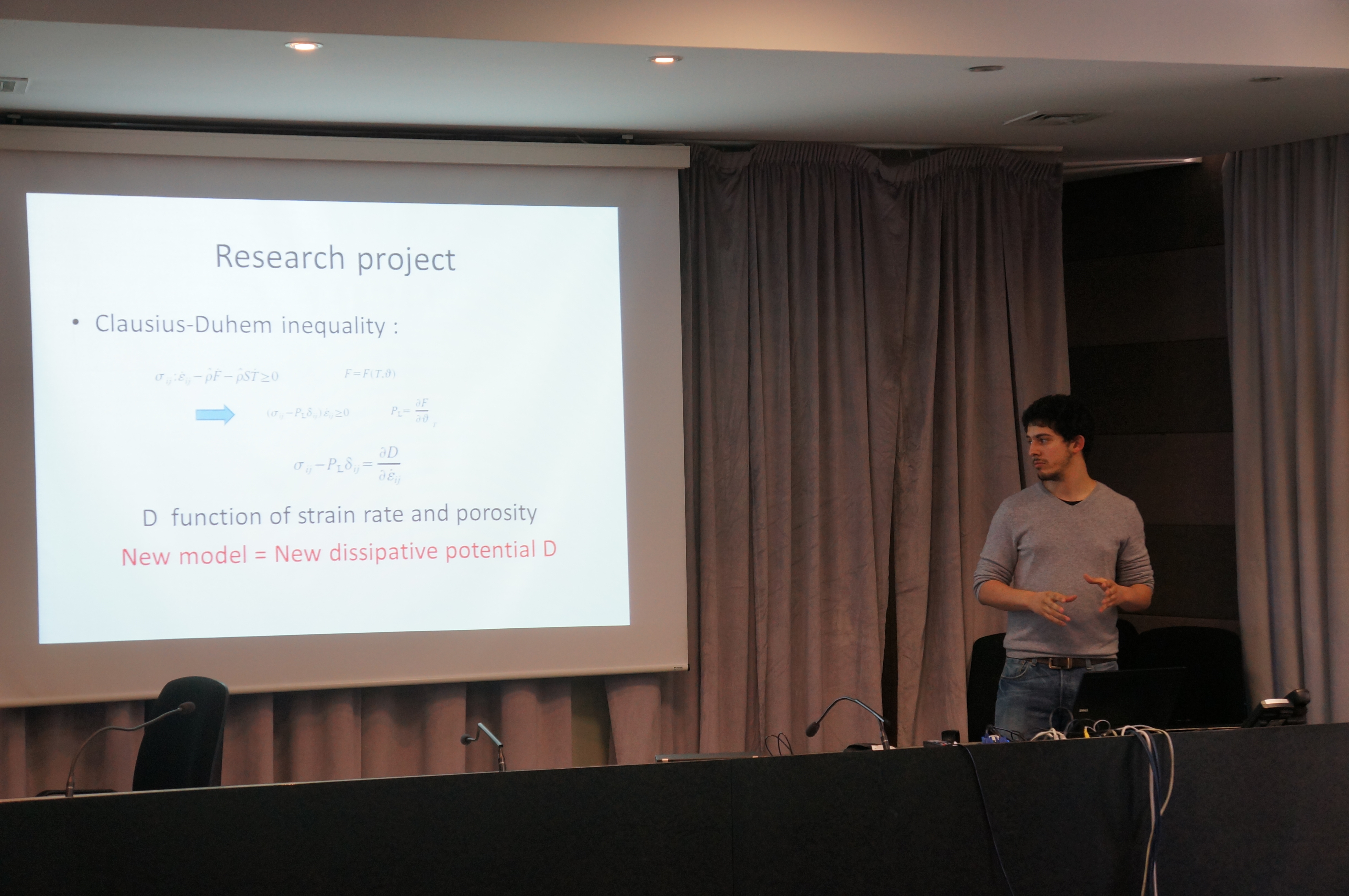
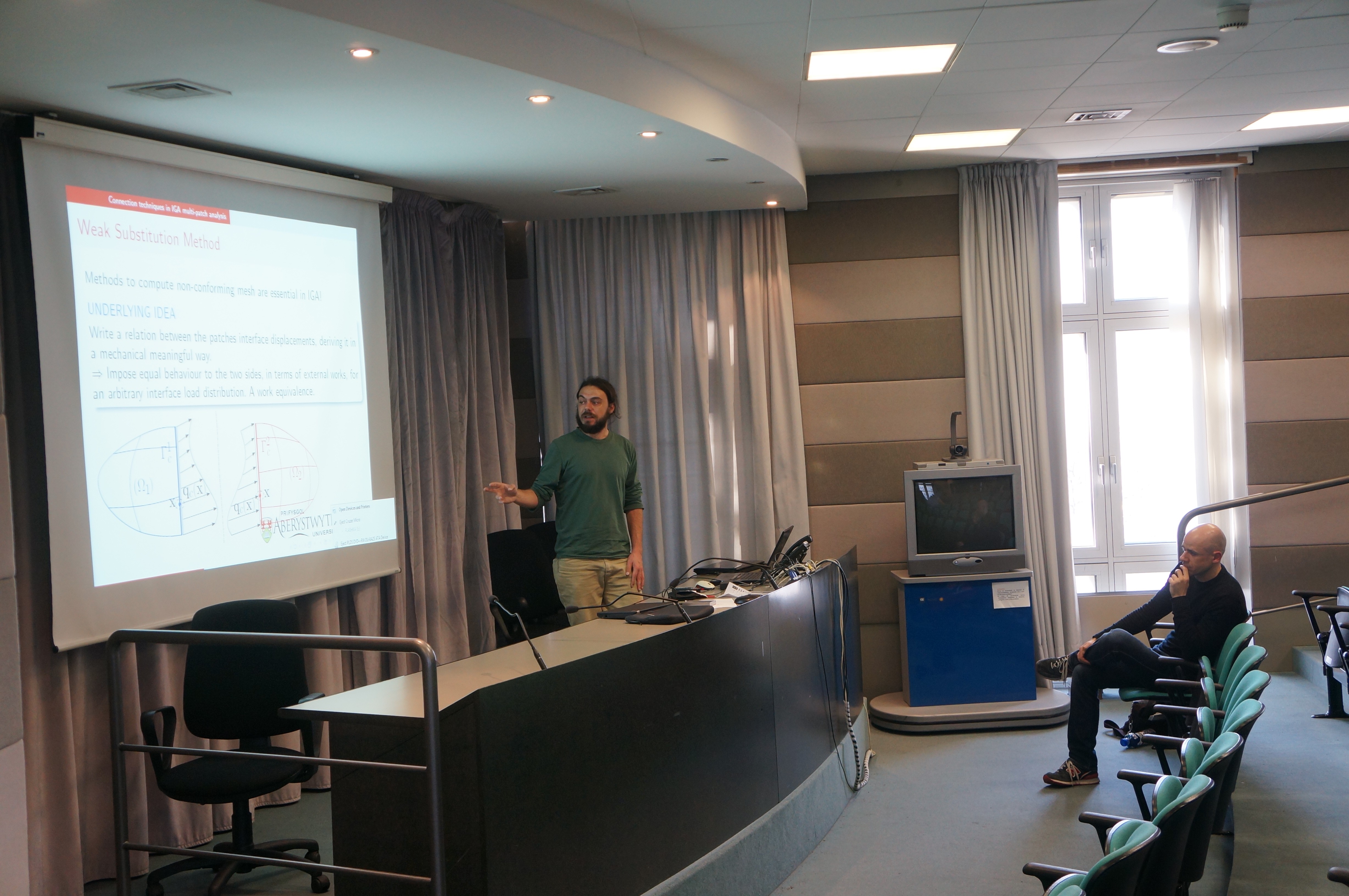
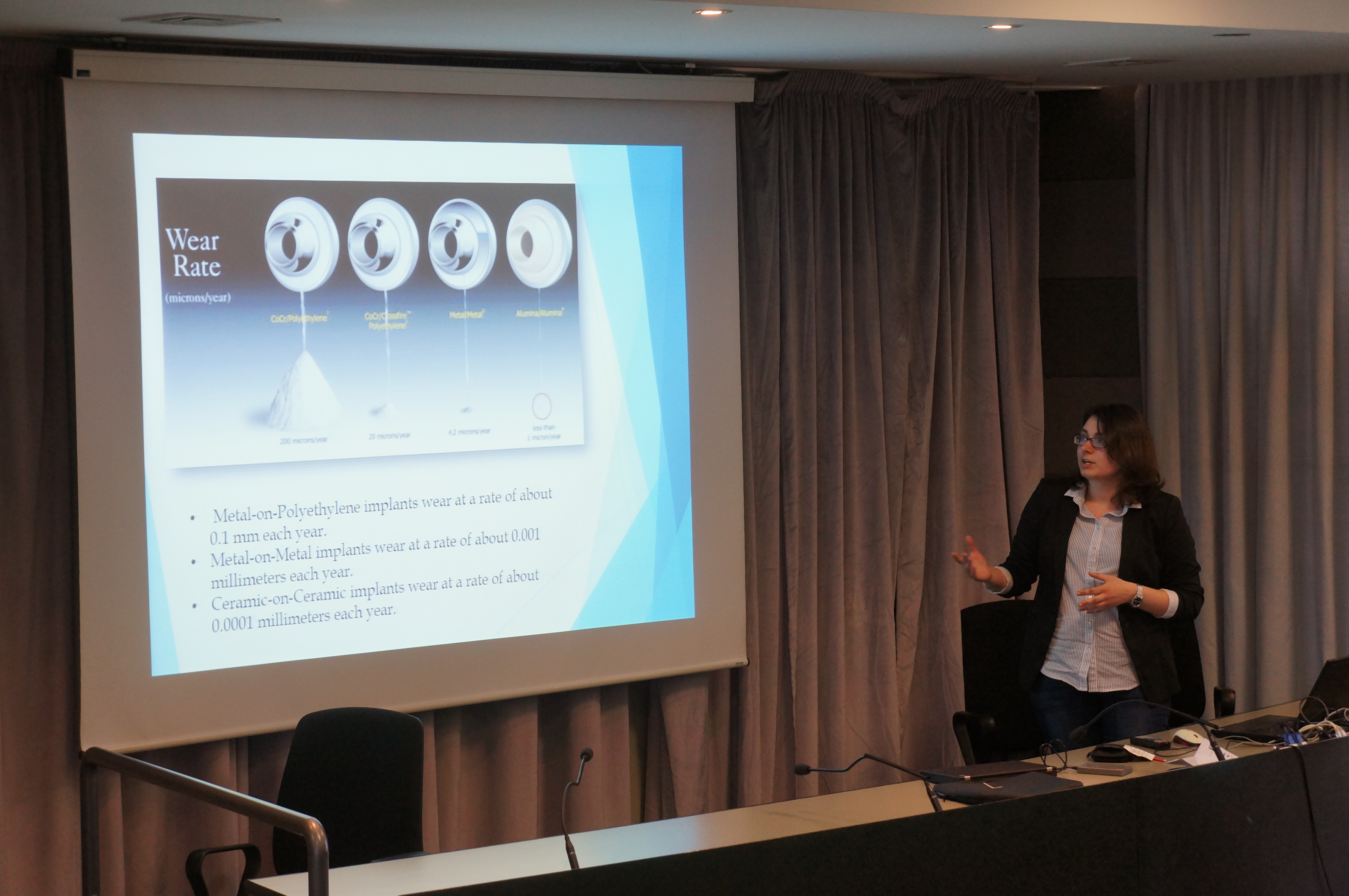
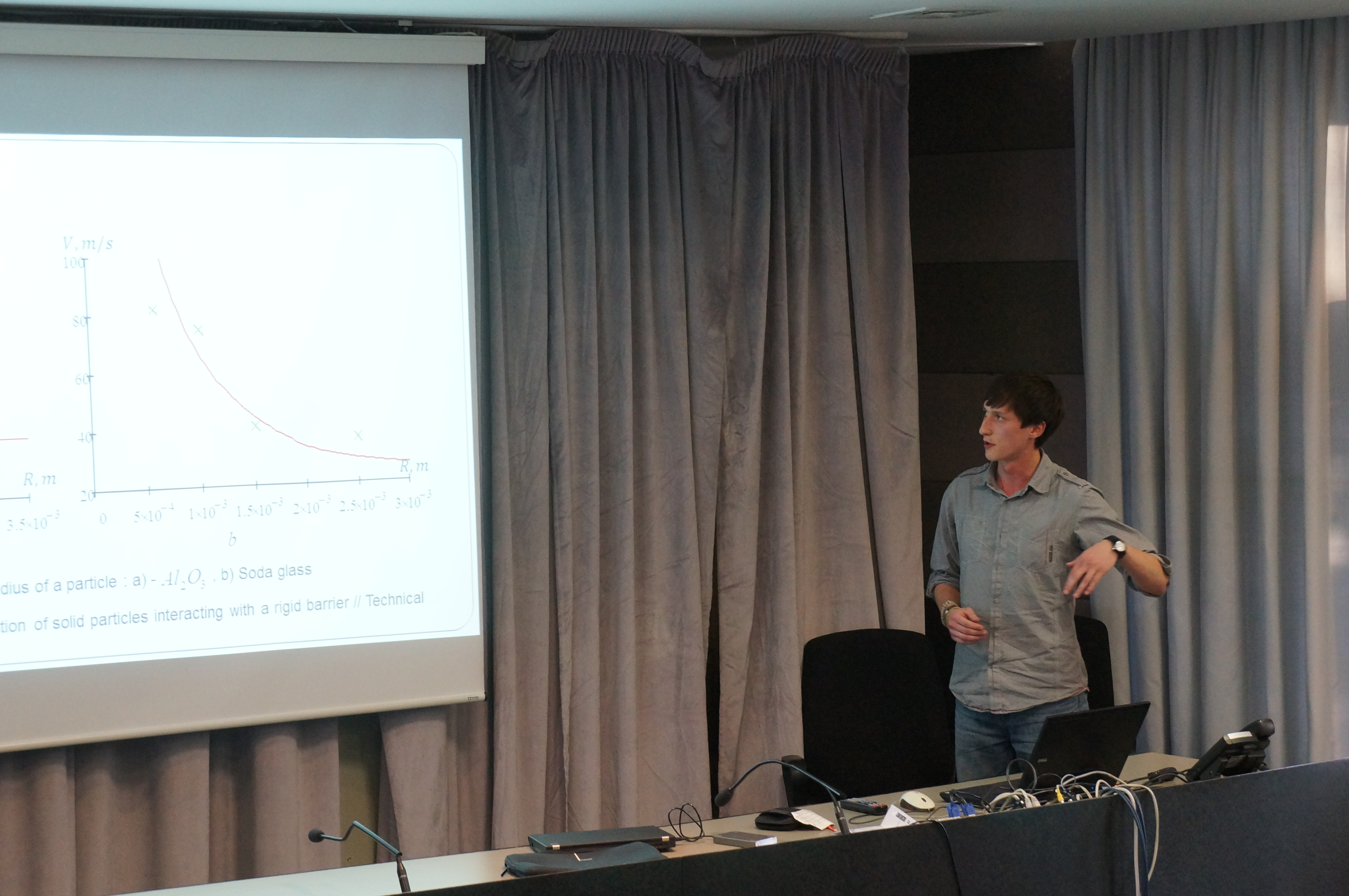
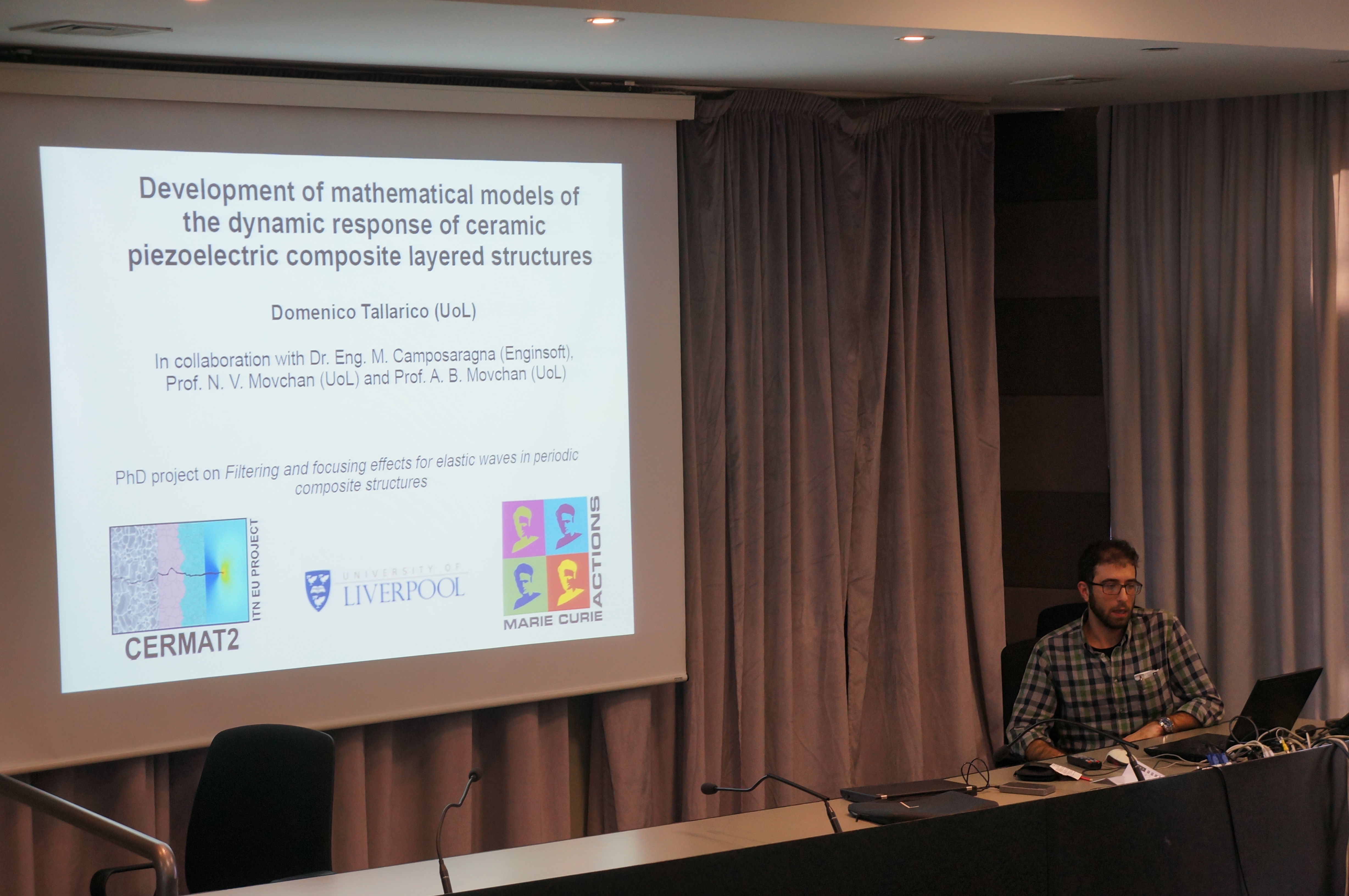
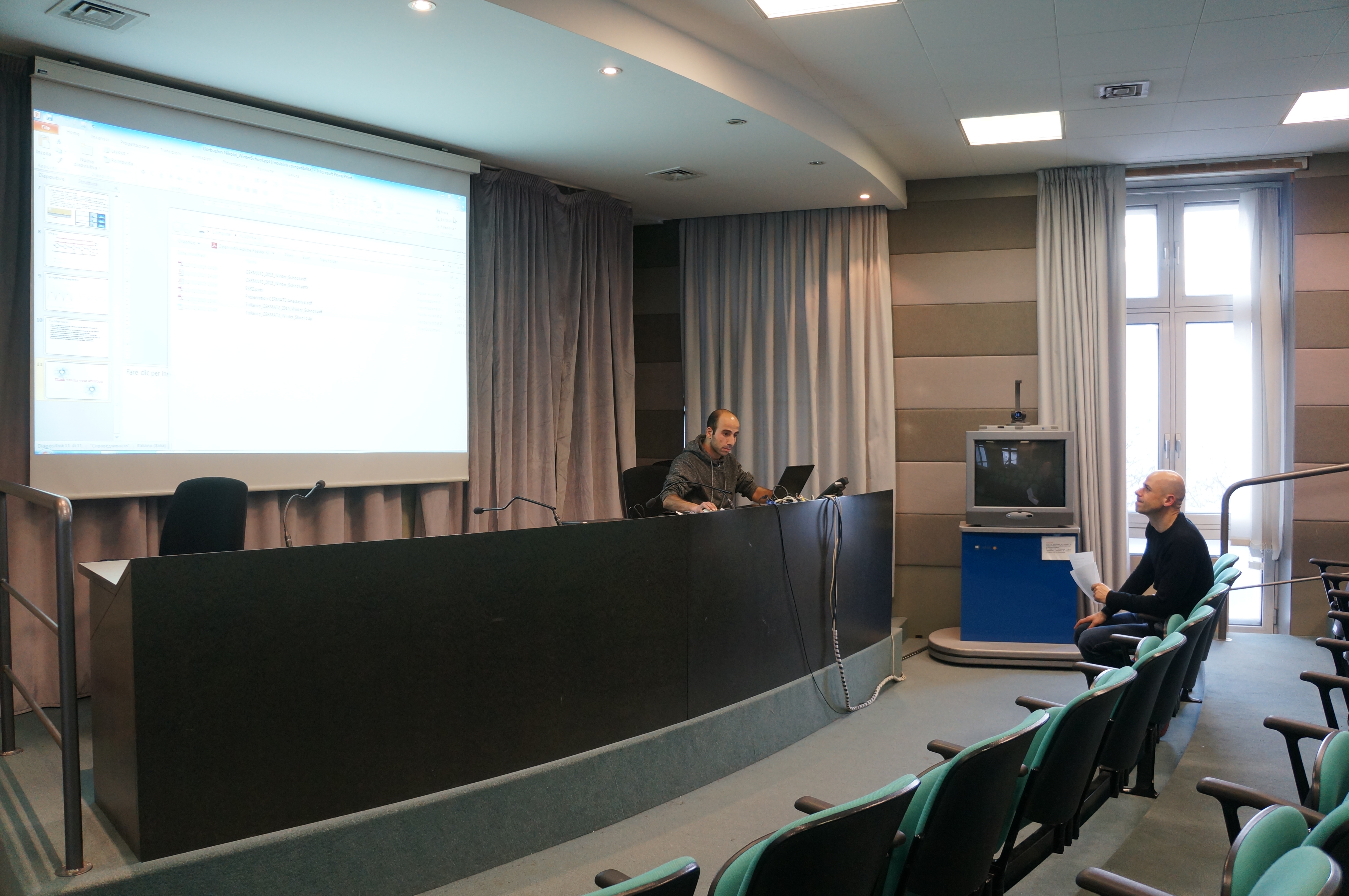
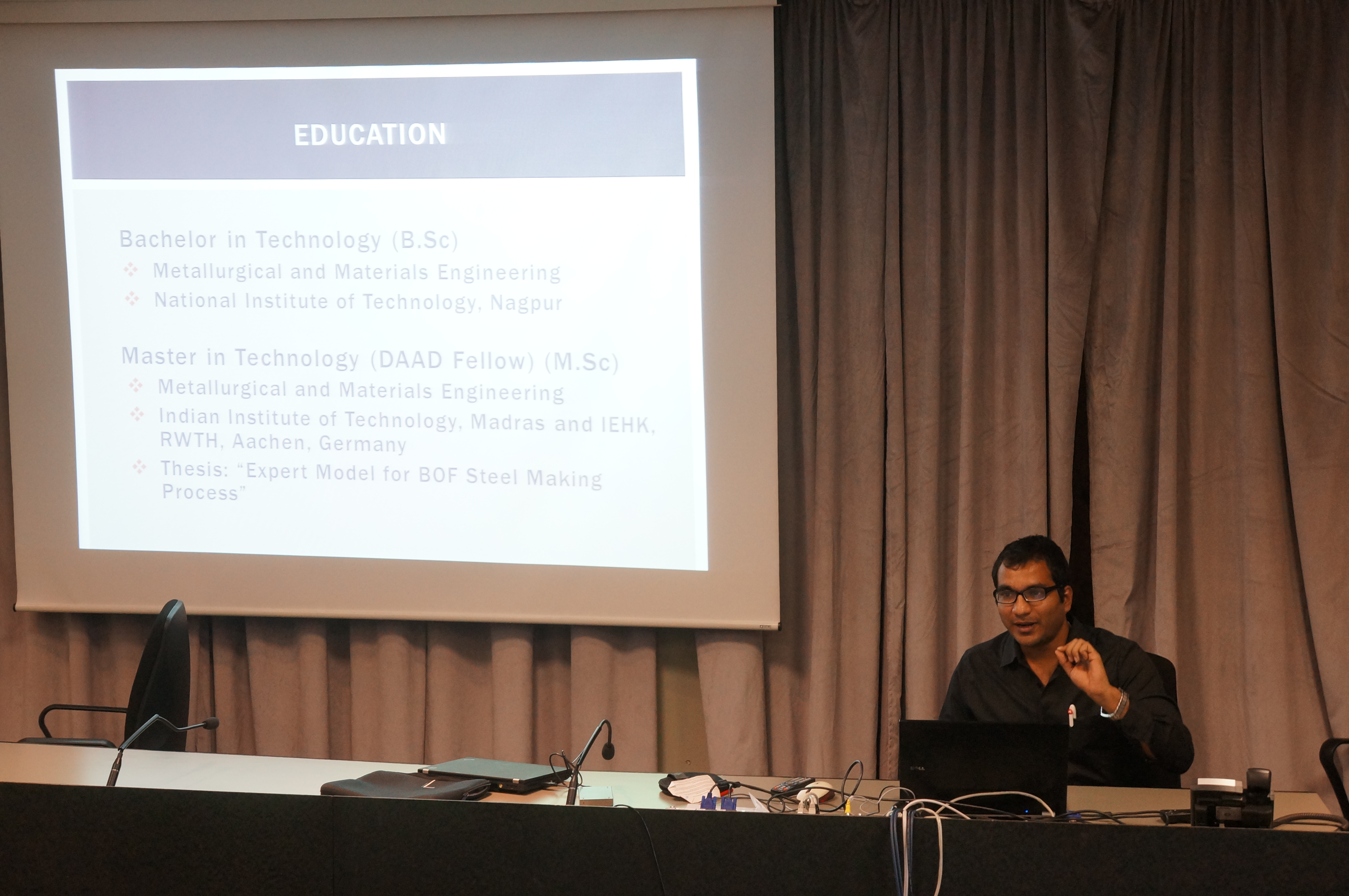
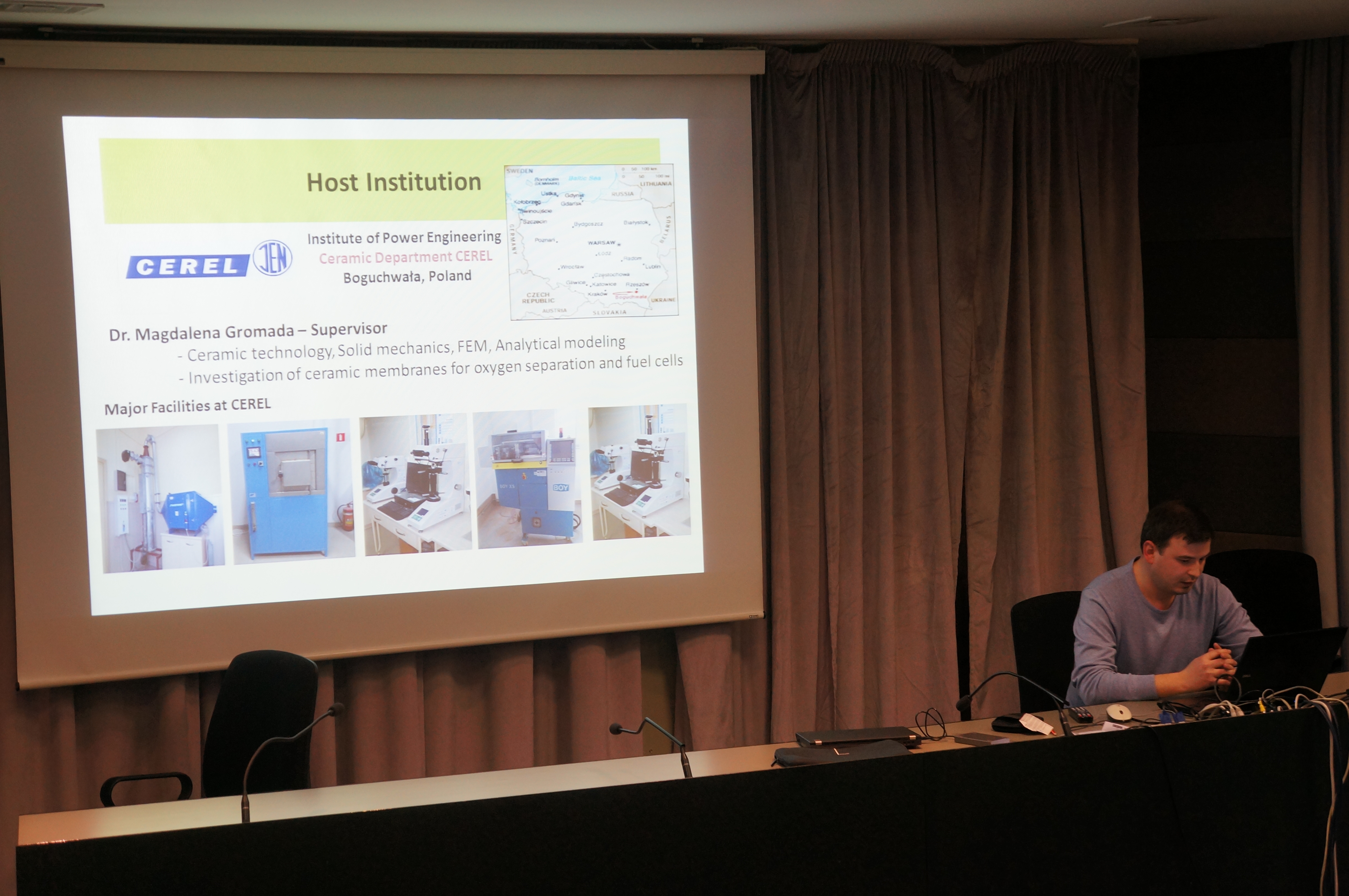
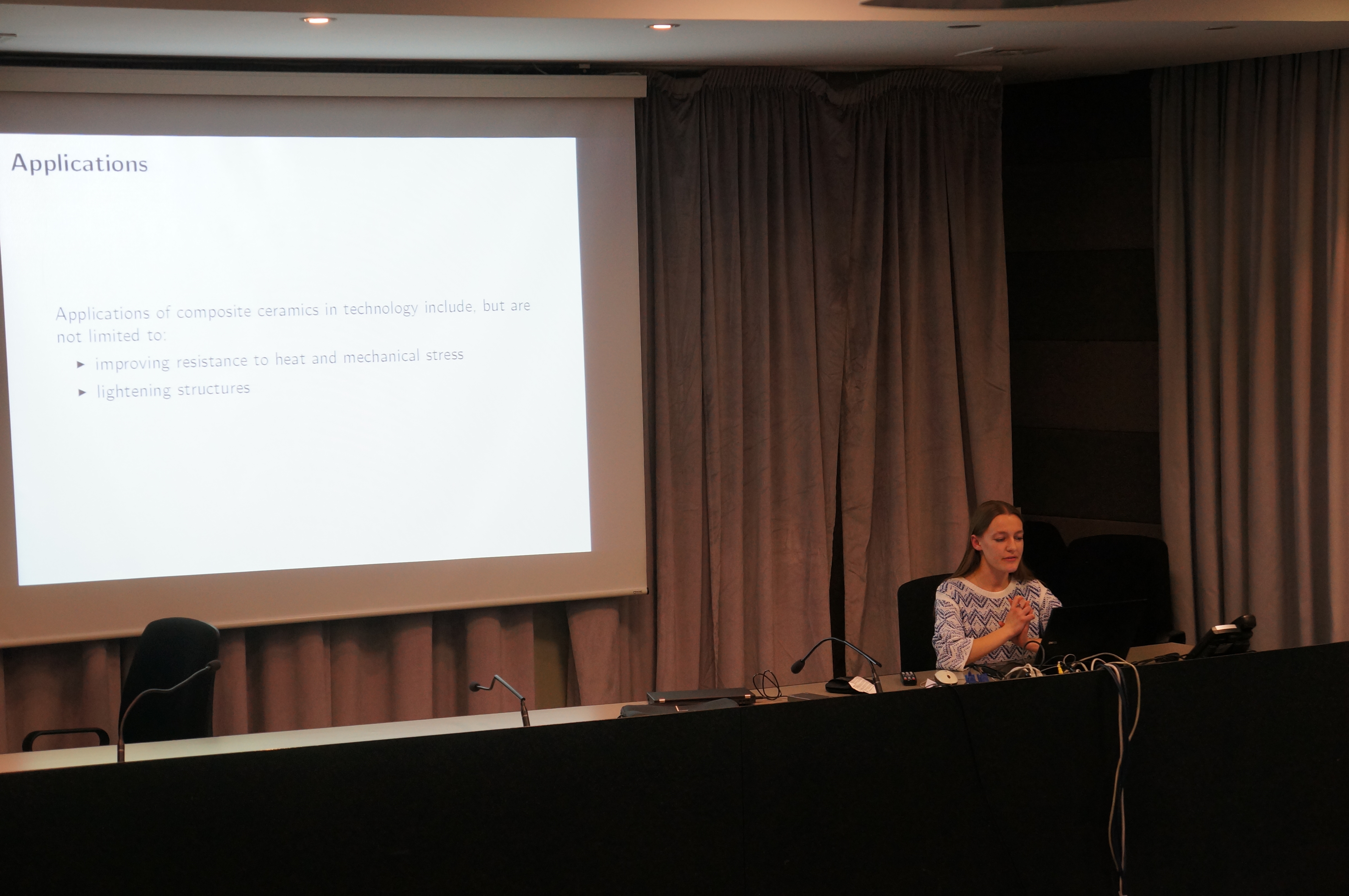
Contacts
Prof. Andrea PiccolroazDipartimento di Ingegneria Civile, Ambientale e Meccanica
Universitā di Trento, via Mesiano, 77 I-38123 Trento (Italia)
Tel: +39 0461 282583
Fax: +39 0461 282599
E-mail: roaz@ing.unitn.it